Impiego del collettore rotante
I collettori rotanti sono organi fondamentali per il corretto funzionamento di tutte quelle macchine che prevedono organi in movimento rotativo. E’ generalmente composto da una parte fissa sulla quale sono predisposte delle connessioni in ingresso, ed una parte girevole che ha una o più connessioni per l’uscita. Lo scopo del collettore è appunto quello di ricevere il “prodotto” (sia esso un liquido, gas, segnale elettrico o altro) in ingresso e distribuirlo in uno o più punti posti in rotazione della macchina stessa.
Tipologie di collettore rotante
Esistono diverse tipologie di collettori rotanti come ad esempio:
- Collettori rotanti elettrici: sono impiegati per la distribuzione di segnali elettrici e/o potenza elettrica.
- Collettori rotanti elettro-pneumatici: sono analoghi a quelli elettrici ma presentano un canale aggiuntivo per la distribuzione di aria compressa
- Collettori rotanti per fluidi: sono idonei per la distribuzione di liquidi
- Collettori rotanti per gas in pressione o vuoto: impiegati per la distribuzione di gas in pressione o vuoto pneumatico.
- Collettori rotanti ibridi: si tratta solitamente di prodotti custom che nascono dalla combinazione delle tipologie precedenti.
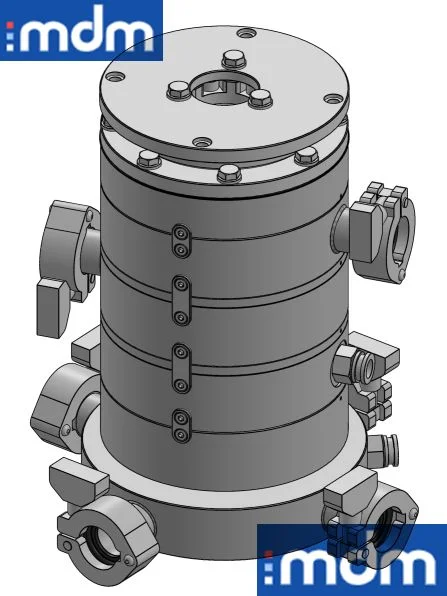
Requisiti di progettazione
Tralasciando i collettori elettrici ed elettro-pneumatici che prevedono numerose varianti in base alla quantità di segnali e potenze in gioco e per i quali sono presenti numerosi prodotti in commercio già preconfigurati, per quanto concerne la realizzazione di un collettore rotante è fondamentale avere a disposizione:
- Natura dei fluidi che devono essere distribuiti: liquidi alimentari, corrosivi, ecc.
- Pressioni di esercizio del fluido e/o presenza di vuoto
- Portate minime e massime richieste
- Definizione delle quantità di ingressi ed uscite richieste
Mentre i primi due punti incidono principalmente sulla selezione dei materiali e sulla geometria dei vari componenti meccanici del collettore, gli ultimi due punti determinano il dimensionamento delle sezioni di passaggio fluidi in ingresso ed in uscita delle due sezioni del collettore.
Selezione dei materiali
La natura dei prodotti da distribuire incide consistentemente nella selezione dei materiali da impiegare per la realizzazione dei diversi componenti del collettore.
Se, ad esempio, il prodotto da veicolare si tratta di un liquido alimentare il materiale più idoneo è sicuramente l’acciaio inox AISI 316L, mentre in caso di prodotti chimici aggressivi è necessario impiegare materiali anti-corrosivi specifici per il tipo di applicazione, ecc.
Lo stesso criterio deve essere adottato per selezionare adeguatamente le tenute in modo che rispettino i criteri di igienicità dal punto di vista sia meccanico che chimico.
In caso di veicolazione di fluidi in pressione o sotto vuoto, le guarnizioni dovranno essere in grado di sopportare le deformazioni in modo da assicurare la corretta tenuta in entrambe le circostanze.
Linee guida per la progettazione
- Oltre alla natura dei prodotti è necessario tenere in considerazione anche il punto di installazione del collettore stesso. Ad esempio se i prodotto da veicolare non richiede l’impiego di acciaio inossidabile, ma andrà installato in una zona della macchina che viene a contatto con liquidi di lavaggio, è bene prevedere ed impedire la possibilità di ossidazione dei componenti esterni del collettore.
- Le guarnizioni a tenuta rotante tendono ad usurarsi precocemente quando la finitura superficiale non è perfettamente liscia. Per ovviare a questo inconveniente i componenti rotanti del collettore possono essere rivestiti nella zona di strisciamento con un riporto ceramico. Questo riporto, oltre ad essere chimicamente inerte nei confronti dei fluidi con il quale viene a contatto, consente una rettifica molto precisa ed una levigatura accurata.
- E’ necessario predisporre delle “spie” che consentano di individuare prontamente l’eventuale perdita di tenuta di ogni singola guarnizione.
- E’ bene prevedere punti di iniezione e di uscita per la lubrificazione dei cuscinetti interni qualora fosse necessaria. Il percorso del grasso non deve essere messo in comunicazione con le guarnizioni dedicate alla tenute dei canali; se questo rischio esiste è necessario prevedere delle tenute aggiuntive che isolino il percorso del grasso che evitano la contaminazione del fluido.
- Molte volte il collettore viene installato su punti della macchina difficilmente accessibili pertanto, per facilitare le operazioni di manutenzione, è necessario prevedere una soluzione di montaggio/smontaggio rapido di tutti i componenti da movimentare per portare a termine l’operazione nel minor tempo possibile.
- Nel caso di collettori per il trasporto di liquidi alimentari, bisogna tenere in considerazione tutte le linee guida per la progettazione Clean-Design, che si traduce in questo caso nel considerare accuratamente le geometrie dei particolari ed il comportamento delle guarnizioni sottoposte a soluzioni, pressioni, temperature diverse a seconda della fase di esercizio della macchina (produzione, processo CIP, ecc.).
- Prevedere un punto di ancoraggio che funga da anti-rotazione della parte fissa del collettore
- Se si desidera combinare due collettori, ad esempio abbinando un elettrico ad uno per fluidi, è necessario prevedere su quest’ultimo (oltre ai necessari fori di fissaggio) un adeguato passaggio centrale non solo per il cavi ma anche per gli eventuali connettori.
Un passo verso il successo
Progettiamo soluzioni personalizzate per le tue esigenze.